Hydraulic Oil Basics: Everything You Need to Know
Understanding Hydraulic Oil: Properties and Importance
Hydraulic oil is a specific type of fluid engineered to transfer power within hydraulic systems while minimizing wear and tear. Unlike typical lubricants, hydraulic oils must handle extreme pressure without breaking down. They play three primary roles:
- Power Transmission: Hydraulic oils act as a medium to transfer energy, enabling heavy machinery and equipment to perform powerful movements with precision.
- Lubrication: It provides lubrication for components, reducing friction and wear, which helps extend machinery life.
- Cooling and Cleaning: Hydraulic oil absorbs heat generated during operation and prevents system overheating. It also carries contaminants away from components, protecting them from damage.
Key Properties of Hydraulic Oil
Several critical properties define the performance of hydraulic oil:
- Viscosity: The thickness or fluidity of oil determines its flow at varying temperatures. Higher viscosity means thicker oil, which is essential for high-pressure conditions.
- Oxidation Stability: High resistance to oxidation reduces sludge formation, which keeps systems cleaner and reduces maintenance.
- Thermal Conductivity: Effective cooling is ensured by high thermal conductivity, which allows the oil to absorb and dissipate heat.
- Anti-Wear Properties: Additives in the oil help protect components from excessive wear, improving durability.
Essential Guide to Hydraulic Oil: How It Works and Why It Matters
Application of Hydraulic Oil
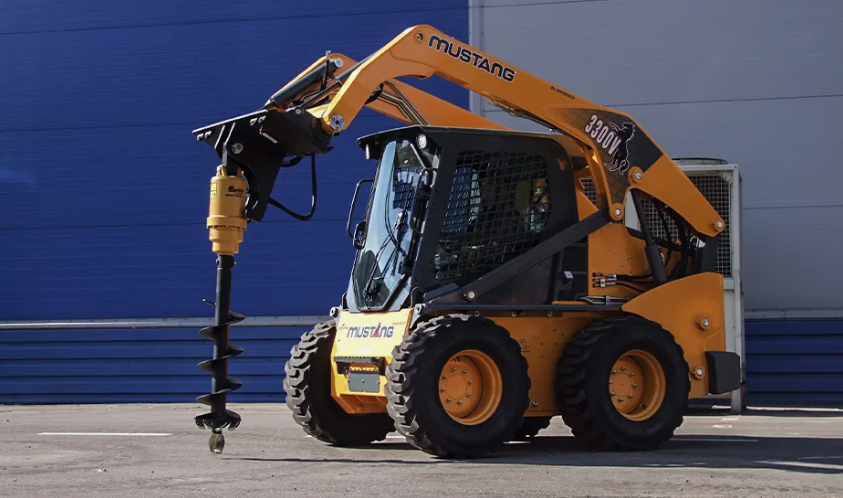
Hydraulic oil is indispensable in numerous industries, playing a pivotal role in equipment performance, longevity, and safety. Here are key applications:
Construction and Heavy Machinery: Hydraulic oil powers excavators, loaders, bulldozers, and cranes, facilitating lifting, digging, and moving heavy loads. It ensures efficient energy transfer for hydraulic cylinders and controls, keeping these machines productive under heavy-duty conditions.
Agriculture: In tractors, harvesters, and other farming equipment, hydraulic oil enables essential functions such as lifting, pushing, and steering. It helps these machines operate in varied weather conditions while handling high-pressure tasks like plowing and harvesting.
Manufacturing and Industrial Machinery: In presses, injection molding machines, conveyors, and robotic arms, hydraulic oil is critical for maintaining precision and stability. It allows the controlled movement of parts and high-pressure applications needed in industrial automation.
Automotive Industry: Hydraulic oil is used in automotive systems like brakes, transmissions, and power steering, allowing controlled power transfer for smoother operation. It ensures safety, responsiveness, and performance, especially under variable driving conditions.
Aerospace: Hydraulic oil is used in aircraft landing gear, flight control systems, and cargo doors. The oil’s stability under extreme pressure and temperature conditions makes it ideal for aircraft operation and safety.
Marine Industry: Ships and boats use hydraulic oil in systems like steering, deck machinery, and winches. It ensures smooth maneuverability and reliable operation in the challenging marine environment.
Mining: Hydraulic oil supports hydraulic drills, loaders, and lift trucks in mining applications, where high pressure and tough conditions are constant. It helps prevent equipment wear and provides reliable performance under harsh conditions.
Renewable Energy: In wind turbines and hydroelectric plants, hydraulic oil is used for controlling blade pitch and other operations. It ensures efficient energy production while managing high pressure and variable environmental conditions.
Forestry: Logging equipment, like feller bunchers, skidders, and harvesters, relies on hydraulic oil for powerful cutting, lifting, and loading capabilities. The oil’s efficiency under high-pressure conditions is essential for sustained, reliable operation in remote environments.
Food Processing: Certain specialized hydraulic oils are safe for use in food-grade applications, such as processing and packaging machinery. They ensure hygienic, controlled movement without contamination risks.
Hydraulic oil’s versatility and adaptability to high-pressure environments make it a key component in a wide array of applications, powering essential operations across industries.
Why Does Hydraulic Oil Get Hot?
One common issue in hydraulic systems is overheating, which can reduce oil life and affect equipment performance. Here’s why hydraulic oil may heat up:
- Overloaded Systems: High-pressure and overworked systems generate more heat as oil circulates at high speed.
- Inadequate Cooling: If the cooling system isn’t performing well, the oil won’t cool down efficiently, leading to increased temperatures.
- Incorrect Oil Type: Using oil that’s too thin or thick for your system can generate excess heat, causing system strain.
When hydraulic oil overheats, it can oxidize faster, reducing its lifespan and creating deposits that lead to blockages in the system. Proper cooling solutions, regular system checks, and using the right oil are essential to prevent overheating.
How to Check Hydraulic Oil Quality
Maintaining hydraulic oil quality is essential for system efficiency. Here are steps to assess your hydraulic oil quality:
- Visual Inspection: Look for changes in color, clarity, or the presence of particles. Clean hydraulic oil should appear clear without cloudiness or sediments.
- Contamination Testing: Use sampling techniques to check for contaminants like water, dirt, or metal shavings. Contamination can indicate system leaks or worn components.
- Viscosity Measurement: Use a viscometer to check if the oil’s thickness aligns with the recommended level. Changes in viscosity often indicate thermal degradation.
- Odor Test: Burnt or unusual smells can indicate overheating or oxidation, which warrants an oil change or system check.
When to Check Quality: Regular checks, ideally every few months, help in identifying early signs of oil degradation or contamination. For high-demand systems, more frequent testing may be necessary.
Key Differences Between Hydraulic Oil and Engine Oil
Hydraulic Oil Additives: Enhancing Performance and Protection
Signs It's Time to Change Your Hydraulic Oil
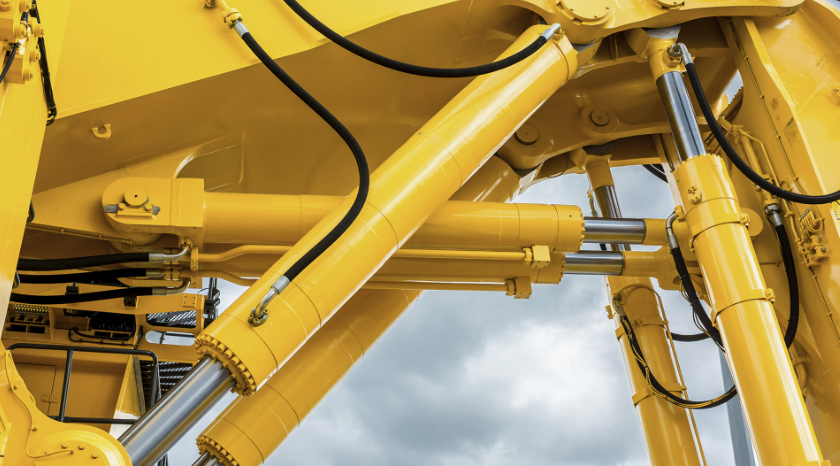
How to Reduce Hydraulic Oil Temperature
Managing hydraulic oil temperature is crucial for system reliability and efficiency. Here are some effective methods:
- Use Heat Exchangers: Heat exchangers are designed to transfer excess heat from hydraulic oil to cooler fluids, maintaining a steady temperature.
- Enhance Ventilation: Ensure proper airflow around equipment, as restricted air circulation can trap heat, leading to higher oil temperatures.
- Choose the Right Oil Grade: Selecting oil with the appropriate viscosity for the operating temperature helps prevent excess friction and heating.
- Regular Maintenance: Checking filters, vents, and fans ensures that the system operates without restrictions that could lead to overheating.
- Maintain Correct Oil Levels: Low oil levels can lead to overheating since there’s less oil to absorb and dissipate heat.
By keeping hydraulic oil temperatures within the recommended range, you reduce wear and tear on system components and improve oil lifespan.
Which Hydraulic Oil is Thicker: 32 or 46?
One common question is about the difference in thickness, or viscosity, between ISO VG 32 and 46 hydraulic oils. Here’s a breakdown:
- ISO VG 32: With a lower viscosity, VG 32 oil flows more easily and is often used in low-pressure environments or systems that operate in cooler temperatures.
- ISO VG 46: VG 46 is thicker and works better under higher temperatures and pressures, as its viscosity ensures a consistent lubricating film.
When choosing between these grades, consider the operating environment and equipment requirements. For example, VG 46 is more suitable for heavy-duty applications or equipment that runs at high temperatures, while VG 32 is ideal for systems needing quicker oil flow under lower temperatures.
Choosing the Right Hydraulic Oil for Your System
Selecting the correct hydraulic oil is a vital decision that affects performance, efficiency, and the lifespan of your equipment. Consider these factors when choosing hydraulic oil:
- System Requirements: Follow the manufacturer’s recommendations for oil type, viscosity, and other specifications.
- Operating Temperature: Choose an oil that performs reliably at the temperatures your equipment will encounter.
- Load and Pressure Conditions: For high-pressure systems, use oils with higher viscosity, such as VG 46, for better protection and reduced wear.
- Additives for Extra Protection: Look for oils with anti-wear, anti-foam, and anti-corrosion additives to enhance system protection and reduce maintenance needs.
Using the right hydraulic oil enhances efficiency, reduces breakdown risks, and can lead to cost savings by extending equipment and oil service life.