Let’s Start Work
Together
Please feel free to contact us. We will get back to you with 1-2 business days. Or just call us now.
Industrial Oils: A Necessary Commodity for Modern Industries
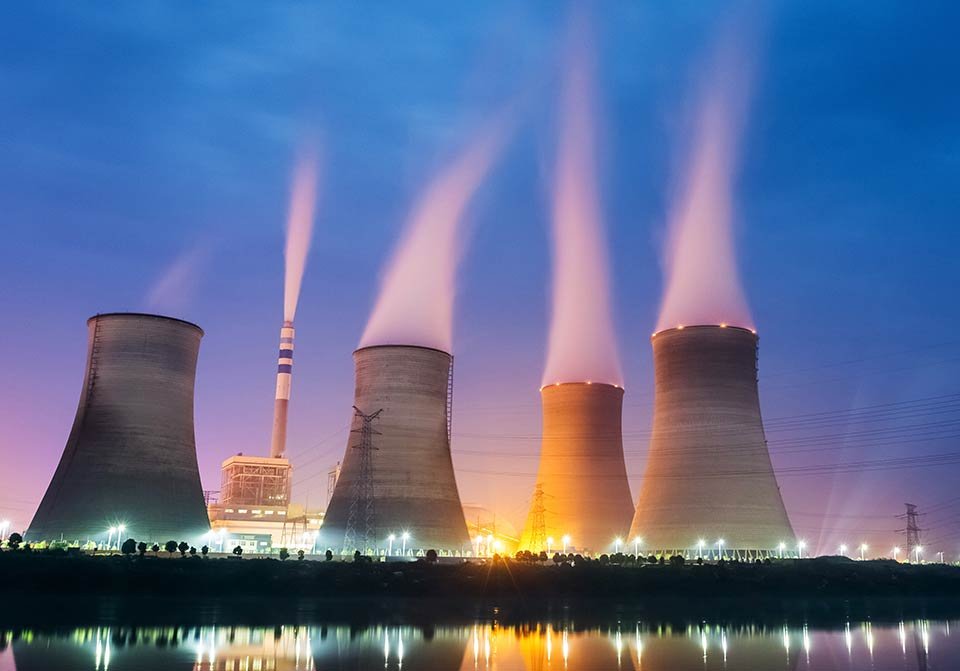
Industrial oils refer to liquids that are used in various industrial applications, such as lubrication, processing, and energy production. These oils can be derived from petroleum, synthetic sources, or natural sources like plants and animals.
Importance:
Industrial oils play a crucial role in modern industries by facilitating smooth operations, reducing wear and tear on equipment, improving efficiency, and enhancing product quality. They are essential in industries such as automotive, manufacturing, construction, food processing, and energy production. Without industrial oils, many of these industries would face significant challenges in terms of productivity, safety, and environmental sustainability.
Types of Industrial Oils
- Mineral oils (petroleum-based): These oils are derived from crude oil and are the most commonly used industrial oils due to their low cost and wide availability. They are suitable for a variety of applications, including lubrication, hydraulic fluids, and gear oils. Mineral oils can be further classified based on their viscosity, such as light, medium, and heavy oils.
- Synthetic oils (chemically produced): These oils are chemically produced using synthetic base stocks, such as polyalphaolefins (PAOs) or esters. Synthetic oils offer several advantages over mineral oils, including higher performance in extreme temperatures, better oxidation stability, and lower volatility. They are commonly used in high-performance applications, such as aviation lubricants and food processing equipment.
Properties of Industrial Oils: Key Factors for Performance and Safety
This is the measure of a fluid’s resistance to flow. Industrial oils are classified based on their viscosity, which affects their lubricating and flow properties. Higher viscosity oils are suitable for applications where high load-carrying capacity is required, while lower viscosity oils are better for applications where low friction and easy flow are necessary.
These properties determine an oil’s resistance to oxidation and aging over time. Oxidation can lead to the formation of acids, sludge, and varnish deposits, which can cause equipment damage and reduce oil performance. Aging resistance ensures that the oil maintains its original properties over time, even in harsh operating conditions.
Applications of Industrial Oils
- Lubrication: Industrial oils are used as lubricants in various machinery and equipment to reduce friction, wear, and heat generation. Examples include hydraulic fluids for hydraulic systems, gear oils for gears, and compressor oils for compressors.
- Processing: Industrial oils are utilized in various industrial processes as carriers, binders, or lubricants. For instance, they are used in plastic molding, printing inks, and food processing.
- Energy production: Industrial oils find applications in energy production processes such as hydraulic fracturing fluids for oil and gas extraction and steam cycle oils for power generation.
- Environmental protection: Industrial oils are used in various environmental applications such as bioremediation agents for cleaning up contaminated sites and spill control products for containing and cleaning up oil spills.
Conclusion and Future Outlook
FAQs
Industrial oils reduce friction and wear in machinery by forming a thin film between moving parts that separates them and reduces the contact area between them. This reduces the amount of heat generated during operation and prevents wear on the parts due to friction.
Industrial oils prevent rust and corrosion in machinery by forming a protective layer on metal surfaces that prevents moisture and oxygen from coming into contact with the metal. This prevents rust and corrosion from forming on the metal surfaces.
Industrial oils can significantly affect the efficiency of machinery by reducing friction, wear, and heat generation. When properly applied and maintained, industrial oils can extend the life of machinery components, reduce maintenance costs, and improve overall equipment efficiency (OEE) by reducing downtime due to breakdowns or failures.
Industrial oils play a critical role in ensuring the reliability of machinery components by providing lubrication, protection against corrosion, and cooling properties that prevent wear, damage, or failure due to friction, heat generation, or corrosion. Properly applied and maintained industrial oils can extend the life cycle of machinery components by preventing wear and corrosion that would otherwise lead to failure or breakdowns over time. This results in improved equipment reliability and reduced maintenance costs over time due to lower repair or replacement costs associated with component failures or breakdowns.
Industrial oils can have a significant impact on the cost-effectiveness of machinery operations by affecting factors such as maintenance costs, energy consumption, and equipment reliability. Properly applied and maintained industrial oils can reduce maintenance costs by preventing wear and corrosion on machinery components, reducing downtime due to breakdowns or failures, and extending equipment life cycles. They can also reduce energy consumption by improving equipment efficiency due to reduced friction and wear, which results in lower operating costs over time.