Hydraulic systems are widely used in manufacturing and construction industries along with aviation. They possess hydraulic oil at the heart that transmits power while acting as lubricant for system components. Hydraulic oil, however, alone is quite inefficient to sustain performance in the long run. It is here when hydraulic oil additives come into action. Hydraulic oil additives are chemical agents combined with hydraulic oil to enhance performance, extend the service life of the equipment, and cut down the operational costs. They increase the oil’s resistance to oxidation, inhibit its wear, and keep it at the appropriate viscosity over a wide range of operating conditions.
Choosing the right hydraulic oil additive really makes all the difference as far as the performance and the lifespan of the hydraulic system are concerned. With hundreds of different additives available in the market today, knowing what to look for is still the most important thing so that your system operates smoothly, efficiently, and always reliably. So, let’s talk about what are the important properties of hydraulic oil additives, factors to be considered, and common mistakes in choosing the right additive.
Understanding Hydraulic Oil Additives
Hydraulic oil additives are chemical products added to hydraulic fluids to improve its functionality. These additives specifically focus on the factors that create problems in the hydraulic system such as oxidation, corrosion, foam formation, and wear. If the additives are not present, the hydraulic oil’s performance would become significantly inferior and require more maintenance. The additives may protect equipment against their corrosion and will leave a protective layer on metals that prevents friction and does not allow contaminant deposits to build.
There are several different types of additives and it all has a distinct purpose and what it provides for hydraulic system performance and machinery benefits. Some are designed for viscosity improvement, while others are corrosion or wear preventive. The choice of additive which would best suit the operating conditions of the hydraulic system will depend on the demand of the particular machinery. Selecting the right combination of additives will surely provide proper performance, minimize wear, and extend the life of your hydraulic system.
Key Properties to Look For
When selecting a hydraulic oil additive, the following are some of the most important properties to look out for. These properties ensure hydraulic oil performs well under different conditions and provides essential protection to your machinery.
1. Viscosity Index Improvers
VI improvers are additives that keep the oil viscosity at an excellent range of temperatures. Hydraulic systems operate frequently under variable temperatures, and the fluid should maintain its fluidity at low temperatures while holding its viscosity at higher temperatures. VI improvers assist the fluid to flow steadily, and thus the hydraulic system would work effortlessly without experiencing temperature variability issues.
2. Anti-wear additives
Wear is one of the major problems to which hydraulic systems are susceptible. Ongoing friction between metal parts might become a source of wear. Wear will compromise the efficiency and the lifespan of the system. Anti-wear additives form a protective layer on the surface of the metal, therefore, reducing direct contact between moving parts. That reduces friction, prevents damage, and extends the life of the hydraulic components.
3. Rust and Corrosion Inhibitors
Moisture usually finds its way into hydraulic systems and can lead to rusting and corrosion. Rust and corrosion inhibitors are added to hydraulic oils to prevent the formation of rust on metal surfaces. Additives are made to provide protection to the interior components against corrosion so that the system is kept in operating condition and, therefore, the risk of failure of the system is reduced.
4. Antioxidants
Oxidation is a chemical reaction occurring as hydraulic oil combines with oxygen. This reaction generates more sludge, varnish, and other harmful substances destroying hydraulic parts. The antioxidative agents within hydraulic lubricants have an inhibiting effect on the oxidation reaction and maintain long-living clean oil.
5. Demulsifiers
Why Additives Are Important
Hydraulic oil additives play an essential role in the preservation of the hydraulic system’s performance and life. They solve all those problems that normally reduce the efficiency of the system, such as wear and tear, corrosion, and oxidation. Without proper additives, hydraulic oil breaks down faster, which means its maintenance period is more frequent, downtime longer, and repair costlier.
Additives allow hydraulic systems to operate under extreme conditions, such as high temperatures, loads, and contamination. The right selection of additives can help you optimize the performance of your hydraulic system and reduce wear and tear on your components, thus lengthening the life of your equipment as well. This not only saves money but ensures that it runs smoothly, therefore lower the probability of costly breakdowns.
Choosing Additives for Different Environments
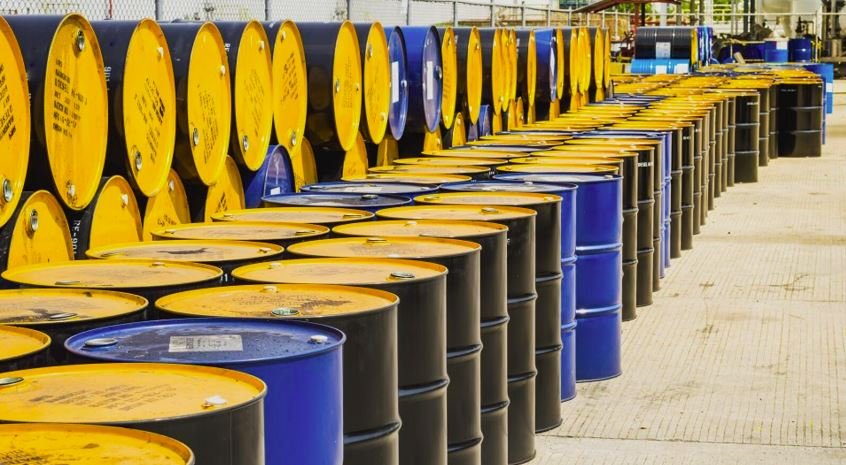
Operating environment determines the kind of hydraulic oil additive to be selected. The point is that different kinds of operating environments pose different kinds of challenges, and the right additive will solve many problems.
1. Operating in High Temperature
Hydor oils thin out in high temperatures, which can weaken the lubricating and protective nature against components. Viscosity index improvers and antioxidants are considered to be essential additives when the oil works in extreme conditions with such temperatures. Through this, it keeps the viscosity of the oil and prevents oxidation, thus being an effective protector of hydraulic systems at such high temperatures.
2. Cold Weather Applications
In cold weather, hydraulic oil becomes thick enough, which makes the system work harder to operate. In cold temperatures, viscosity index improvers are also important since they allow the flow of oil at lower temperatures. Also in cold weather, anti-wear additives are important in preventing grinding of metal parts when the oil is thicker.
3. Contaminated Systems
Compatibility with Hydraulic Systems
Of course, not all additives can be used in every hydraulic system. The additives have to be chosen with care and must be prepared for the components in your hydraulic system as well as their operating conditions. The wrong additive could thus mean a loss of performance and increased wear that eventually leads to system failure. You have to therefore be sure to follow the manufacturer’s recommendations in choosing an additive. Then you have to check if the additives are compatible with materials used in the hydraulic system.
Some additives deteriorate seals, hoses, and other nonmetallic parts. For example, some anti-wear additives reduce the life of seals that cause leaks and even other problems. Additives shall be selected for compliance with all parts of the hydraulic system in question.
Additive Standards and Certifications
For the best hydraulic oil additive, their products should also meet industry standards and certifications. The best additives to buy would be those certified by any such organization as the American Petroleum Institute (API) or the International Organization for Standardization (ISO). This would ascertain standards of quality and performance, thus giving confidence in how the product will function.
Some even offer their quality-testing and certification procedures to warrant their additives. Nonetheless, avoid such additives and purchase only from reliable manufacturers who could demonstrate their intention to offer only the best quality stuff.
Common Mistakes in Choosing Additives
Several common mistakes people make when choosing hydraulic oil additives are listed below. Most consider only the price of the additive. Although this may sound reasonable, low-price additives usually result in poor performance, high wear, and costly repairs later.
It also fails to consider specific operating conditions regarding hydraulic systems. Different environments require different additives, and hence, making a wrong additive will reduce the efficiency of the system, hence increasing the risks of damage. Always consider the operating temperature, load, and contamination levels when selecting an additive.
Lastly, some people just fail to refer to the additive manufacturer’s recommendations during the selection of an additive. Your hydraulic system manufacturer knows best what additives should mix well with your equipment. Not adhering to the recommendations can cause the system to fail and even void warranties.
Latest Innovations in Hydraulic Oil Additives
The hydraulic oil additive field has constantly been on the threshold of improvement with new technologies that aim to maximize performance and increase efficiency. Recently, nano-additives were found to be the latest innovation: teeny-tiny particles intended to upgrade the oil’s lubricating properties. These additives reduce friction at the microscopic level, and they extend the life of hydraulic components and improve system efficiency even further.
Innovations in environmentally friendly additives. These are the developments focused more on sustainability by industries. More sustainable additives are more biodegradable and non-toxic. Their performance is similar to that of traditional additives, but with a reduced impact of the hydraulic system on the environment.
Which Hydraulic Oil Additives Are Essential for Optimal Machinery Operation?
Some essential additives in hydraulic oil include anti-wear agents, oxidation inhibitors, corrosion inhibitors, and viscosity improvers. Anti-wear additives form a protective layer on metal surfaces, reducing friction, while oxidation inhibitors prevent fluid breakdown due to oxygen exposure. Corrosion inhibitors protect metal parts from rust, and viscosity improvers ensure the fluid maintains the right thickness across a range of temperatures.
What Are the Best Hydraulic Oil Additives for Extreme Temperature Conditions?
For machinery operating in extreme temperatures, viscosity improvers and pour point depressants are essential. Viscosity improvers help the oil maintain fluidity at both high and low temperatures, ensuring proper lubrication. Pour point depressants prevent the oil from becoming too thick in cold conditions, allowing for easier startup and smooth operation in freezing environments.
Final Thoughts
Choosing the right hydraulic oil additive is essential for maintaining the performance and longevity of your hydraulic system. By understanding the key properties of additives and considering the specific operating conditions of your system, you can select the best additive to optimize performance and protect your equipment. Remember to always follow the manufacturer’s recommendations and look for certified additives from reputable manufacturers.
The right additive can help you prevent wear, reduce downtime, and save money on repairs, ensuring that your hydraulic system operates efficiently and reliably for years to come.